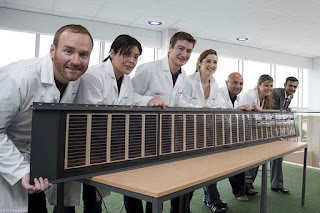
New breakthroughs in solar technology have been announced which could mean a complete game changer in the way electricity is generated.
The technology involves printing a new type of solar cell onto building materials, such as steel and glass, and allowing them to generate electricity.
The chief announcement is the result of joint ventures between Australian company Dyesol and, in Wales, Tata Steel, and in America Pilkington Glass.
Researchers are being cautious as to the timescale, but it is estimated that in about five years time industrial production on a large scale could begin.
Speaking at a recent conference on solar power, James Durrant of the Department of Chemistry and Energy Futures Lab at Imperial College London, said “If just 10% of Tata's annual steel output were coated with DSSC, this would represent the output capacity equivalent to a 1GW nuclear power station per year".
Dye-sensitised solar cells (DSSC)
These 'dye-sensitised solar cells' (DSSC) employ a photoelectrochemical system similar to that employed by plants to capture solar energy.
In the manufacturing process, a nanocrystalline titanium oxide film plus a sensitiser dye are printed onto glass, polymer or steel and covered with glass or plastic.
Modules made from the cells currently have efficiencies up to 8% depending upon a compromise between stability and cost, but cells in the lab have reached 13% efficiency, and Dyesol is confident they can reach 10% under mass-production conditions in five years time.
DSSC has the following advantages over conventional silicon photovoltaic modules:
- it can output a constant operating voltage in all light conditions, including low light and dappled conditions typical of urban and city environments, making it an ideal renewable resource for closely packed buildings
- it has an optimum working temperature of 40o-50oC, unlike silicon PV, which becomes less efficient at higher temperatures
- it uses little energy in manufacture due to the low temperature processes and absence of high vacuum technology needed for second generation technologies (thin film PV)
- due to the nanoparticulate nature of the titanium dioxide, modules can generate electricity from light from any direction, removing the need for them to be pointed directly at the sun
- it can be produced in a range of natural colours and light transmission effects including transparent, translucent or opaque
- it uses no polluting dopant
- the ability to produce a constant operating voltage in all light conditions
- it is ideal for integrating into building cladding.
The race to mass production
Many companies are racing to produce this type of cell at an industrial scale.
Notable organic and dye-sensitized solar cell (DSSC) developers include, beside Dyesol: Eight19, EPFL, G24i, Heliotek, Konarka (printing large molecule polymers), Mitsubishi, Peccell, Plextronics, Solarmer, SolarPress and SolarPrint.
SolarPrint is also developing nanomaterials and processes to print the cells onto polymer substrates. Other researchers are experimenting with printing on fibreglass.
Eight19 Limited has raised $5 million from the Carbon Trust and Rhodia to develop plastic organic solar cells. The name "Eight19" refers to the time it takes sunlight to reach the earth.
The reason why Dyesol is a front-runner is because of its teamwork with Pilkington and Tata Steel. These joint ventures are already ahead of the game in terms of applying coatings on a continuous roll, as opposed to a batch process, output.
Existing coatings applied to steel include galvanising layers to prevent rust, colours, anti-static, and self cleaning layers, all of which are guaranteed for 40 years.
Tata's Rodney Rice, speaking from their DSSC Demonstration Roof at the PV Accelerator in Shotton, North Wales, where the process is being tested, told Energy and Environmental Management, "we use high speed large scale coating, on steel rolls 1.5m wide, put through at a speed of 200 metres per minute.
"This adds up to 200 million square metres of steel per annum, of which half ends up on buildings. If we assume 10 to 20% of this is on a roof or wall and the PV is operating at between 8 and 10% efficiency, then this will easily equate to 1 GW per year.
“We are developing our knowledge of printing coatings to printing the ability to generate electricity and to steel. It uses reasonably straightforward materials which are reliable, simple to apply and easy to scale up as there is no vacuum and fewer people involved.
"This means it has the perfect attributes for the mass-market and the technology will work well in northern Europe where there are large surface areas of roof tops."
The Dyesol-Tata partnership has obtained considerable support from the Welsh Government, and over the last four years has spent £11 million on R&D.
“Lowering the price is the objective and we are now developing processes that will allow us to do this in manufacture," continued Rodney.
"Initially steel rolls will be one metre wide with 10% efficiency leading to a production of 400 MW per year," he said.
Tata use coated steel and coated polymer electrodes, whereas Pilkington are using coated glass electrodes.
In America, the Pilkington-Tata joint venture has won $1 million from the Ohio Third Frontier Fund, and intends to complete its proof of concept project for large glass substrate panels by the summer of 2012.
Its chief competitor, American company Konarka’s technology, is a photo-reactive polymer material invented by Konarka co-founder and Nobel Prize winner, Dr. Alan Heeger.
This can be printed or coated inexpensively onto flexible substrates, again using roll-to-roll manufacturing.
It can work indoors too, capturing ambient light.
Like Dyesol, Konarka has recently entered a partnership agreement with a steel producer, ThyssenKrupp Steel Europe to develop solar steel roof, facades and other construction elements for building-integrated photovoltaics (BIPV) in Germany.
Dr. Lars Pfeiffer, head of quality and development at the Color/Construction unit. "Unlike conventional silicon-based photovoltaic systems, the joint solar solution will not need to be mounted on a raised structure but will integrate smoothly into the building envelope. We look forward to providing the valuable, added benefits of solar to our customers at a low cost."
Challenges
Some problems remain to be solved. For example, could it survive 25 years?
Rodney Rice says at the moment Tata can produce several square metres, and has installed a 15 m² demonstration roof can be used to test the output and performance.
“We are now developing our abilities in the process, durability, assembly and manufacturing," he said.
It is the dye which is crucial for the generation of the electricity from light. Different dyes are being researched all over the world.
“We are looking for the perfect dye," said Rodney. “The ability to capture light energy from a wide range of wavelengths is required in order to maximise efficiency. More than half research in world is looking at new dyes, extending wavelengths, including into the infrared," he said.
Dyesol is now ramping up more aggressive performance targets under a revised Technology Road Map, to achieve grid parity at an earlier date.
Whichever company is the first to successfully produce cladding for buildings which can cheaply produce electricity, will find themselves at the head of a multibillion dollar market.
Even supposing half of what these companies are claiming is hyperbole, then we are perhaps looking at a ten year timescale rather than five years before the technology reaches mass production.
Even so, this would be before the anticipated timescale for new nuclear power stations to come online. So, the big question is: would it obviate the need for new nuclear power by rendering it uncompetitive?
Thinking about the ease and convenience of producing, installing and using this technology at the point of use, it is clearly going to be a massive game changer.
The missing part of the jigsaw is still electricity storage, since, although this technology can produce energy at night time from indoor lighting, this will not meet peak demands.
This topic will be the subject of another special Low Carbon Kid technology report in 2012.
2 comments:
Wow what a great technology, this really has the potential to completely change the solar panels industry in gloucester. Just think of how much roof space there is in a city and how easy it would be to print these off and attach them to the roof. I would love to know what is the current cost of production of these? I would imagine it not cheap for a 200 meters squared of this stuff.
As the article says, it is not going to be commercially available for 3-5 years.
Post a Comment